Keys to a compliant vehicle maintenance file
- Brandon Wiseman
- Oct 2, 2023
- 6 min read
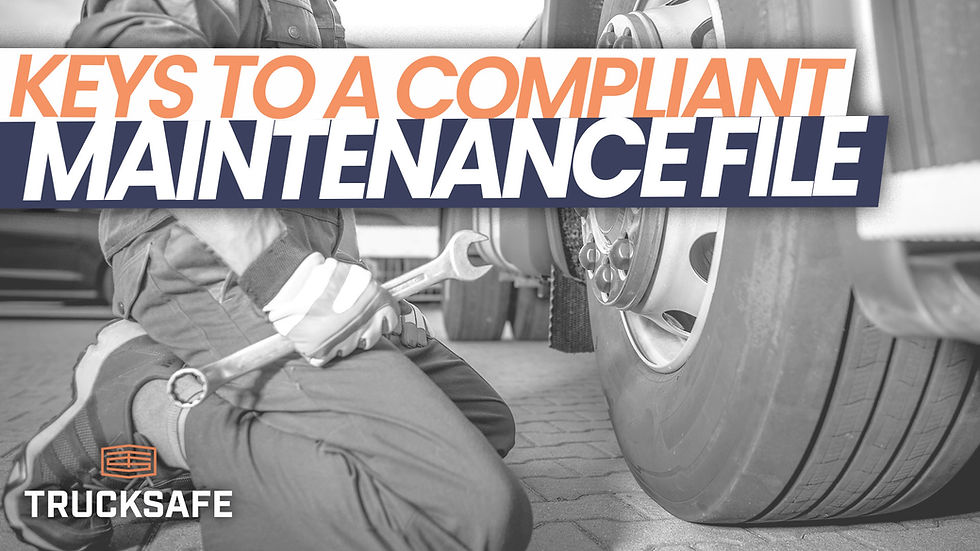
As a regulated fleet, there's no shortage of records you're required to maintain: driver qualification files, accident registers, insurance info, driver logs, drug/alcohol test results, just to name a few!
One particularly important group of documents on that list are those pertaining to the maintenance of your commercial vehicles. Part 396 of the Federal Motor Carrier Safety Regulations compels motor carriers to properly inspect and maintain their equipment and document their efforts to do so in compliant maintenance files. As with any other regulated files, these records are subject to audit and can really cost if you if not properly maintained.

Why's this the case? Well, it should go without saying that operating poorly maintained, heavy vehicles on public roadways can be dangerous. Unfortunately, FMCSA data suggests that, on average, around 22% of all commercial vehicles stopped for roadside inspections get placed out of service for serious maintenance-related defects. Certainly some of these issues stem from normal road wear & tear, but the reality is that many of the issues could and should have been discovered by the carrier and/or its driver through routine inspections. Maintenance-related recordkeeping obligations are the way the FMCSA requires carriers to keep tabs on this.
As a preliminary matter, Part 396 of the federal safety regulations require motor carriers to generate and maintain maintenance files on all commercial motor vehicles that are subject to its control for 30 or more days, which essentially encompasses all owned equipment and rented/leased equipment with terms of longer than 30 days. See 49 CFR 396.3(b). In another article, we break down specifically what types of vehicles are included in the regulatory definition of a "commercial motor vehicle" or CMV and, thus, subject to this requirement.
But what exactly do the regulations require of fleets when it comes to vehicle maintenance files? Let's break it down...
Basic identifying information
The first and most basic items that every compliant vehicle maintenance file must contain per Part 396 of the federal safety regulations are basic identifying information for the subject vehicles (both power units and trailers). More specifically, 49 CFR 396.3 requires that carriers keep the following data points for all regulated equipment:
An identification of the vehicle including company number, if so marked, make, serial number, year, and tire size. In addition, if the motor vehicle is not owned by the motor carrier, the record shall identify the name of the person furnishing the vehicle.
In practice, these data points are typically listed on some sort of cover sheet to paper-based maintenance files or on an equipment profile tab in an electronic file. Failing to have any one of these required data points can, and routinely does, lead to problems in an FMCSA investigation. For example, we've been involved in several DOT audits in which carriers have been written up and finesd for failing to keep track of the tire sizes of their commercial vehicles.
Check out our sample vehicle maintenance file cover sheet at the link below:
Periodic (annual) inspection reports
Next up, a compliant vehicle maintenance file must include up-to-date periodic inspection reports for all regulated equipment (again, including power units and trailers). In particular, 49 CFR 396.17 requires motor carriers to, at least annually, have their commercial vehicles inspected pursuant to the criteria set forth in Appendix A to Part 396. These inspections are often referred to as DOT annual inspections, and the reports generated from them must be retained in each vehicle's maintenance file. More specifically, the regulations require carriers to maintain such reports covering the last 14 months, which means carriers must keep the current and last periodic inspection report for each regulated vehicle. A copy of the report, or a sticker evidencing the details of the inspection, must also be kept on the vehicles themselves and produced to law enforcement on demand.
Along similar lines, the regulations also technically require motor carriers to maintain records of inspector qualifications. Indeed, 49 CFR 396.19 provides that "Motor carriers and intermodal equipment providers must retain evidence of that individual's qualifications under this section. They must retain this evidence for the period during which that individual is performing annual motor vehicle inspections for the motor carrier or intermodal equipment provider, and for one year thereafter. However, motor carriers and intermodal equipment providers do not have to maintain documentation of inspector qualifications for those inspections performed as part of a State periodic inspection program." The same holds true for any inspectors carriers use to conduct brake inspections. See 49 CFR 396.25.
For passenger carriers, specifically, the regulations also require you to maintain records of "tests conducted on pushout windows, emergency doors, and emergency door marking lights on buses."
If you need sample annual inspection report forms or inspector qualification records, we have them available here.
Preventative maintenance
Aside from periodically inspecting their commercial equipment, carriers also have a regulatory obligation to systematically maintain and repair it. In other words, carriers must have a preventative maintenance program in place to ensure their vehicles remain in proper working condition at all times.
When it comes to recordkeeping for preventative maintenance, the regulations require carriers to have (1) "a means to indicate the nature and due date of the various inspection and maintenance operations to be performed"; and (2) a record of all such maintenance performed, including the date and nature of the maintenance. See 49 CFR 396.3.
In short, carriers need to have PM schedule for all of their regulated equipment, indicating the frequency at which they will perform any PM services or required inspections. Further, they need to keep records of any such maintenance that is performed (e.g., repair orders, invoices, etc.) in the maintenance files for all of their equipment. Failing to stick to the PM schedule or keep records of the maintenance performed can lead to violations in an audit, and can also create additional exposure in highway accident litigation.
What PM schedule you keep is up to you, but sticking to the recommended schedule set by the equipment manufacturer is often best. Carriers have an obligation to retain preventative maintenance documentation for a period of 12 months from when it was generated.
DVIRs & records of repair
In another article, we break down the driver vehicle inspection report (DVIR) process in detail. In short, whether you’re a property- or passenger-carrying operation, the regulations (49 CFR 396.11) establish a specific process that drivers and carriers must follow when it comes to preparing and submitting DVIRs. The first step, obviously, is that the driver prepares the DVIR, identifying the CMV that was inspected, including any attached trailers, and listing any defects discovered by or reported to the driver. Importantly, this would include situations where a driver becomes aware of a maintenance defect from a third-party such as an officer during a roadsideinspection.
Once the driver prepares the DVIR, he/she must sign it and submit it to the operating motor carrier. This has historically been done on paper, but can also be accomplished electronically. Some of the electronic systems are even set up so that the DVIRs are automatically transmitted to the carrier’s maintenance department, which can help facilitate a quicker turnaround on vehicle repairs. For its part, once a carrier receives a DVIR from a driver that lists a defect likely to affect the safety of the CMV’s operation, it must not allow the CMV to operate again until the defect is corrected. Once it is corrected, then the carrier or its agent (for example, a mechanic) must sign off on the DVIR to certify that the repairshave been made.
Carriers must retain copies of the DVIRs and the repair records in the vehicle’s maintenance file. Once the repair is made and certified, then its important that drivers review the prior day’s DVIR, if any, before operating for the day to ensure any such defects have been corrected. Carriers have an obligation under the regulations to retain DVIRs for a period of 3 months from the date they were generated.
Missing DVIRs are a common contributor to fines and downgraded safety ratings in a DOT audit, so it's critical that carriers and their drivers follow this process.
Conclusion
Generating and retaining up-to-date and complete vehicle maintenance files is a major component of every regulated carrier's DOT compliance program. Failing to keep compliant files can lead to significant fines in an audit and, more importantly, can create significant exposure in highway accident litigation. If you need assistance understanding the vehicle maintenance regulations or auditing your files, please feel free to contact us.
About Trucksafe Consulting, LLC: Trucksafe Consulting is a full-service DOT regulatory compliance consulting and training service. We help carriers develop, implement, and improve their safety programs, through personalized services, industry-leading training, and a library of educational content. Trucksafe also hosts a monthly live show on its various social media channels called Trucksafe LIVE! to discuss hot-button issues impacting highway transportation. Trucksafe is owned and operated by Brandon Wiseman and Jerad Childress, transportation attorneys who have assisted some of the nation’s leading fleets to develop and maintain cutting-edge safety programs. You can learn more about Trucksafe online at www.trucksafe.com and by following Trucksafe on LinkedIn, Facebook, Twitter, and YouTube.